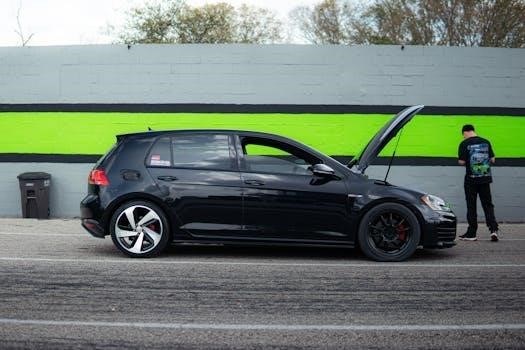
This manual provides guidance for diagnosing and resolving common issues with Ice-O-Matic commercial ice machines. It offers practical steps to ensure your machine operates at peak performance. Utilizing this guide can help minimize downtime.
Ice-O-Matic is a globally recognized brand that specializes in manufacturing commercial ice machines. Their product line includes cubers, flakers, and Pearl Ice machines, all designed with a focus on simplicity, reliability, and ease of use. These machines are built to provide consistent ice production for various commercial applications. With a commitment to quality, Ice-O-Matic machines aim to meet the demands of businesses requiring reliable ice solutions. This manual will help users understand the basic operations of Ice-O-Matic and assist in resolving issues quickly and effectively. The brand is known for its user-friendly approach to ice making. By understanding the fundamental design of these machines, users can better diagnose problems.
Common Issues Overview
Even with high-performance brands like Ice-O-Matic, malfunctions can occur. Common issues include the machine not running, insufficient ice production, and hollow ice cubes. Pump problems and water leakage are also frequent concerns. Understanding the error light system is crucial for identifying the root cause of problems. This manual provides guidance on troubleshooting these common issues. Problems like blocked water lines, clogged evaporators, and malfunctioning components can all lead to operational difficulties. Additionally, environmental factors such as high ambient temperature can impact ice production. This overview aims to prepare users for quickly recognizing and addressing common issues that may arise with their Ice-O-Matic machines.
Machine Not Running⁚ Initial Checks
When your Ice-O-Matic machine fails to start, the initial steps are crucial for diagnosing the problem. Begin by ensuring the ICE/OFF/WASH switch is correctly positioned to “ICE”. A common oversight is neglecting to check if the machine is properly switched on. Verify the power cord is securely connected and inspect it for any visible damage. Confirm that the power outlet is functioning correctly by testing it with another device. These basic checks will help determine if the issue lies with the power supply or an internal component. It is important to rule out these simple causes before attempting more complex troubleshooting steps. This will save time and prevent unnecessary repairs.
Power Supply Verification
A crucial first step when troubleshooting an Ice-O-Matic machine that isn’t running is to verify the power supply. Start by visually inspecting the power cord for any signs of damage, such as cuts or fraying. Next, ensure the cord is firmly plugged into a working power outlet. You can test the outlet by plugging in another device to see if it receives power. If the outlet is functional, use a multimeter to check the voltage at the machine’s power input. Confirm that the voltage matches the machine’s specifications, typically 115V AC. If power is present but the machine still doesn’t run, the problem likely lies within the unit itself and further troubleshooting will be needed.
Pump Issues and Testing
The pump is vital for circulating water within your Ice-O-Matic machine. If you suspect a pump problem, start by visually inspecting it for any damage or obstructions. Listen carefully for any unusual noises coming from the pump during operation; a faulty pump may produce a grinding or whining sound. To further test the pump, ensure it is receiving the correct voltage, typically 115V AC. If the voltage is present, you can try directly connecting the pump to a power supply to confirm if it runs. If the pump does not operate when directly connected, it may need to be replaced. It’s important to identify if the issue is with the pump or any other component of the system.
Hartell Pump Troubleshooting
When troubleshooting a Hartell pump in your Ice-O-Matic machine, begin by checking its power supply; confirm it’s receiving the expected 115V AC. Inspect the pump’s wiring for any loose connections or damage. If power is reaching the pump, listen for unusual noises such as grinding or humming, which might indicate a failing motor. You can attempt to test the pump directly by providing the 115V AC to see if it activates. If it doesn’t start, it’s likely the pump itself is defective. Ensure there are no obstructions in the pump’s inlet or outlet which may impede water flow. If everything else checks out, you may need to consider replacing the Hartell pump with a new one to restore the proper function.
Ice Production Problems
Encountering issues with ice production in your Ice-O-Matic machine can be frustrating, but there are common causes to investigate; If your machine isn’t making enough ice, consider the ambient temperature; excessively high temperatures around the unit can significantly reduce ice output; A blocked water line or clogged evaporator can also hinder ice production. Hollow ice cubes often point to problems with the water supply or the machine’s freezing cycle. If ice production stops entirely, try resetting the machine; this simple step can sometimes resolve minor issues. Understanding the machine’s error light system can also provide valuable clues. Remember to regularly check and clean the machine to prevent these problems from occurring.
Insufficient Ice Production
If your Ice-O-Matic machine is not producing enough ice, several factors could be at play. Start by assessing the ambient temperature surrounding the unit; if it’s too high, the machine’s efficiency will be significantly reduced, leading to lower ice production. Check for any blockages in the water line, which can restrict the flow of water to the ice-making components. A clogged evaporator can also impede ice formation, requiring cleaning or maintenance. Inspect the machine’s settings and ensure they are correctly configured for optimal ice production. If these checks don’t solve the problem, consult the troubleshooting trees or seek professional service. Regular maintenance is key to avoiding these issues.
Hollow Ice Cubes
Encountering hollow ice cubes from your Ice-O-Matic machine often indicates an issue with the water supply or freezing cycle. This problem can arise from low water pressure, preventing the ice from fully forming. Check the water inlet valve for any obstructions or malfunctions, as it controls the amount of water entering the machine. A faulty water level sensor might also cause inadequate water levels during the freezing process, leading to hollow cubes. Verify that the machine is properly leveled, since an uneven surface can disrupt the ice-making process. Finally, inspect the freezing cycle settings to ensure they are appropriate for the environment. Consult the troubleshooting guide if issues persist.
Leakage Problems
Leakage issues in Ice-O-Matic machines often stem from plumbing connections or internal components. When noticing water outside the unit, start by examining all external plumbing lines and connections for any signs of cracks or loose fittings. Pay close attention to the water inlet and drain lines, ensuring they are securely attached. If the leak persists, inspect internal components such as the water pump and reservoir for cracks or damage. A faulty shutoff valve can also cause leakage; if the valve appears compromised, immediate replacement is recommended. Check the drain lines for clogs that might lead to overflow. If you cannot resolve the leak yourself, seek professional help.
Plumbing Issues and Shutoff Valve
Plumbing problems are a common cause of leaks in Ice-O-Matic machines. Begin by carefully inspecting all water lines connected to the unit for any visible damage, cracks, or loose connections. The shutoff valve plays a crucial role in controlling water flow; a malfunctioning valve can cause persistent leaks or prevent water from entering the machine. If the shutoff valve is the source of a leak, attempt to contain it and contact a qualified plumber immediately to repair or replace the valve. Ensuring that all connections are tight and that the shutoff valve functions correctly is essential to prevent water leakage. Regular inspection can prevent future issues.
Error Light System
The error light system on Ice-O-Matic machines provides valuable diagnostic information about the unit’s operational status. Understanding the meaning of different blinking light patterns is essential for effective troubleshooting. These lights signal various issues, such as problems with the water supply, pump malfunctions, or other critical system errors. Consulting the machine’s service guide is crucial to decipher the specific meaning of each blink code. By identifying the error through the light system, users can efficiently pinpoint problems and take the necessary corrective actions. This helps to prevent minor issues from escalating into major malfunctions, ensuring continuous and efficient ice production.
Understanding Blinking Lights
The blinking lights on your Ice-O-Matic machine are not random; they are coded signals indicating specific problems. Each sequence of blinks corresponds to a different issue, which could range from simple problems to more complex system malfunctions. For example, one pattern might indicate a low water level, while another could signal a pump failure or a problem with the refrigeration cycle. To accurately interpret these signals, it’s crucial to refer to the troubleshooting section of your machine’s service manual. This guide provides a detailed explanation of each blink code, helping you to efficiently diagnose the issue and take the necessary steps to resolve it. Ignoring these signals can lead to more severe issues and costly repairs. Always consult the manual for specific blink codes.
Troubleshooting Trees
The service guide for Ice-O-Matic machines employs troubleshooting trees to streamline the diagnostic process. Each tree is designed to address a specific operational problem, such as insufficient ice production or a non-functioning pump. These trees provide a step-by-step approach, guiding you through a series of questions and checks to pinpoint the source of the issue. Starting at the top of the tree, follow the prompts and perform the suggested tests. The process typically involves verifying components like power supply, water lines, and specific parts like the Hartell pump. By systematically working through the tree, you can quickly narrow down the problem and identify the necessary repair or adjustment. This structured method is essential for effective troubleshooting.
Using the Service Guide
The Ice-O-Matic service guide is an essential tool for diagnosing issues. Specifically, section C, often found around page 33 in PDF versions, contains the crucial troubleshooting trees. These trees are organized by problem type, guiding you through a logical sequence of checks and tests. Begin by identifying the primary symptom your machine is exhibiting. Then, locate the corresponding troubleshooting tree within the guide. Follow the steps precisely, verifying each component as instructed. The guide also provides reference to other relevant sections which may contain additional information. The structured approach ensures you don’t miss any crucial steps in the diagnostic process. Utilizing the service guide is critical for efficient and effective troubleshooting.
Preventative Maintenance
Regular preventative maintenance is crucial for the longevity and efficient operation of your Ice-O-Matic machine. Consistent checks and cleaning can prevent many common issues. Inspect the water lines for any signs of leaks or cracks, addressing them promptly to avoid further complications. Clear any blockages in the drains to ensure proper water flow. Periodically clean the evaporator to prevent mineral buildup, which can hinder ice production. Check the bin control switch, ensuring it is clean and aligned correctly for proper dispensing. By proactively maintaining your machine, you can reduce the need for costly repairs and ensure consistent ice production. This approach minimizes downtime and optimizes the performance of your ice maker.
Regular Checks and Cleaning
Implementing a routine schedule for regular checks and cleaning is essential for maintaining optimal performance of your Ice-O-Matic machine. Begin by visually inspecting all water lines for leaks or cracks, addressing any issues immediately. Clear any blockages in the drain lines to ensure proper water flow and prevent backups. Clean the evaporator regularly to remove mineral deposits, which can impede ice production. Examine the bin control switch, ensuring it is clean and aligned correctly to avoid dispensing issues. These simple, routine checks can help identify potential problems before they escalate into major repairs. Regular cleaning also helps maintain the quality of the ice produced. These steps will extend the life of your machine.
Warranty Information
Understanding the warranty coverage for your Ice-O-Matic machine is crucial for cost-effective repairs. To determine if your machine is still under warranty, locate the manufacturing date. If the installation date is not available, check the serial number. This will allow you to determine the manufacture date. If this date falls within the warranty period, any covered repairs may be performed without charge. It’s important to keep all purchase records and documentation readily accessible. Be aware of the specific terms and conditions of the warranty, as different components may have varying coverage periods. Always refer to your warranty documentation for complete information. Knowing your warranty status helps you make informed decisions.
Checking Manufacturing Date
To ascertain your Ice-O-Matic machine’s warranty status, locating the manufacturing date is a critical step. If the installation date is unavailable, you will need to find the machine’s serial number. This serial number encodes the production date. Typically, the manufacturing date is part of the serial number. Refer to your machine’s documentation or Ice-O-Matic’s website for details on how to decode the serial number. Once you have identified the manufacturing date, you can easily determine if the machine is still within its warranty period. This information is vital before initiating any repairs or contacting customer service. Always double-check the decoded date to avoid any misunderstandings. This will ensure you receive the appropriate support.